In the annals of Japanese history, few traditions command as much reverence as the forging of Ni-honto, the legendary Japanese swords that have captured the imagination of warriors, scholars and collectors alike. These extraordinary blades, born from the exacting processes of firing and folding rare steel, are not mere weapons; they are living embodiments of Japan’s rich cultural tapestry, woven with threads of spirituality, artistry and an unwavering pursuit of perfection.
The origins of Japanese swordsmithing can be traced back to the 5th century CE, when the art of forging blades was first introduced to the island nation from Korea and China, along with choice techniques for extracting low-impurity iron sand and combining it with specialised charcoals. However, it was during the Kamakura period (1185-1333 CE) that the craft truly flourished, fuelled by the rise of the revered samurai warrior class and their escalating demand for exceptional swords.
During this pivotal era, swordsmiths emerged as respected artisans, their skills in manipulating rare steel alloys and secret forging techniques carefully preserved and passed down through generations of master-apprentice relationships. Each school, or ryū, developed its own unique methods and guarded traditions, creating a tapestry of diverse styles and approaches linked by a steadfast commitment to purifying and folding the finest sourced steels.
The Sacred Ritual and The Secrets of Nihonto Forging
The creation of a Nihonto is not merely an industrial process; it is a sacred ritual, a symphony of fire, rare steel and the swordsmith’s indomitable spirit. From meticulously sourcing ultra-low-impurity iron sand or pig iron to the final polishing that reveals the blade’s legendary hamon pattern, every step is imbued with profound significance and a deep respect for the ancient traditions that have endured for centuries.
The forging of a Nihonto begins with the sourcing of the finest Japanese steel, refined from rare iron sands or specialised smelting of pig iron to minimise impurities like phosphorus, sulfur and excess carbon. This steel, often originating from the renowned iron sand deposits or tatara smelters of the Yamato region, is carefully layered and folded in a meticulous process known as shitahitsu-kitae.
This intricate technique, which can involve folding and hammering the steel dozens or even hundreds of times, serves to further remove impurities and evenly distribute alloys like tungsten and chromium. This enhances the blade’s strength, flexibility and cutting ability, creating a resilient and formidable weapon that can withstand the rigours of battle with unmatched edge retention.
At the heart of the swordsmith’s forge burns a meticulously-tended flame, fuelled by carefully-chosen charcoal blends that must contain very low levels of sulfur, phosphorus and other impurities. This specialised charcoal fire, requiring highly precise air intake, is the catalyst that transforms the layered steel into a blade of unparalleled strength, edge integrity and beauty.
The swordsmith’s mastery over these forging fires is a testament to their dedication, as the introduction of even minuscule amounts of impurities can compromise the blade’s structure and iconic sandblasted hamon pattern.
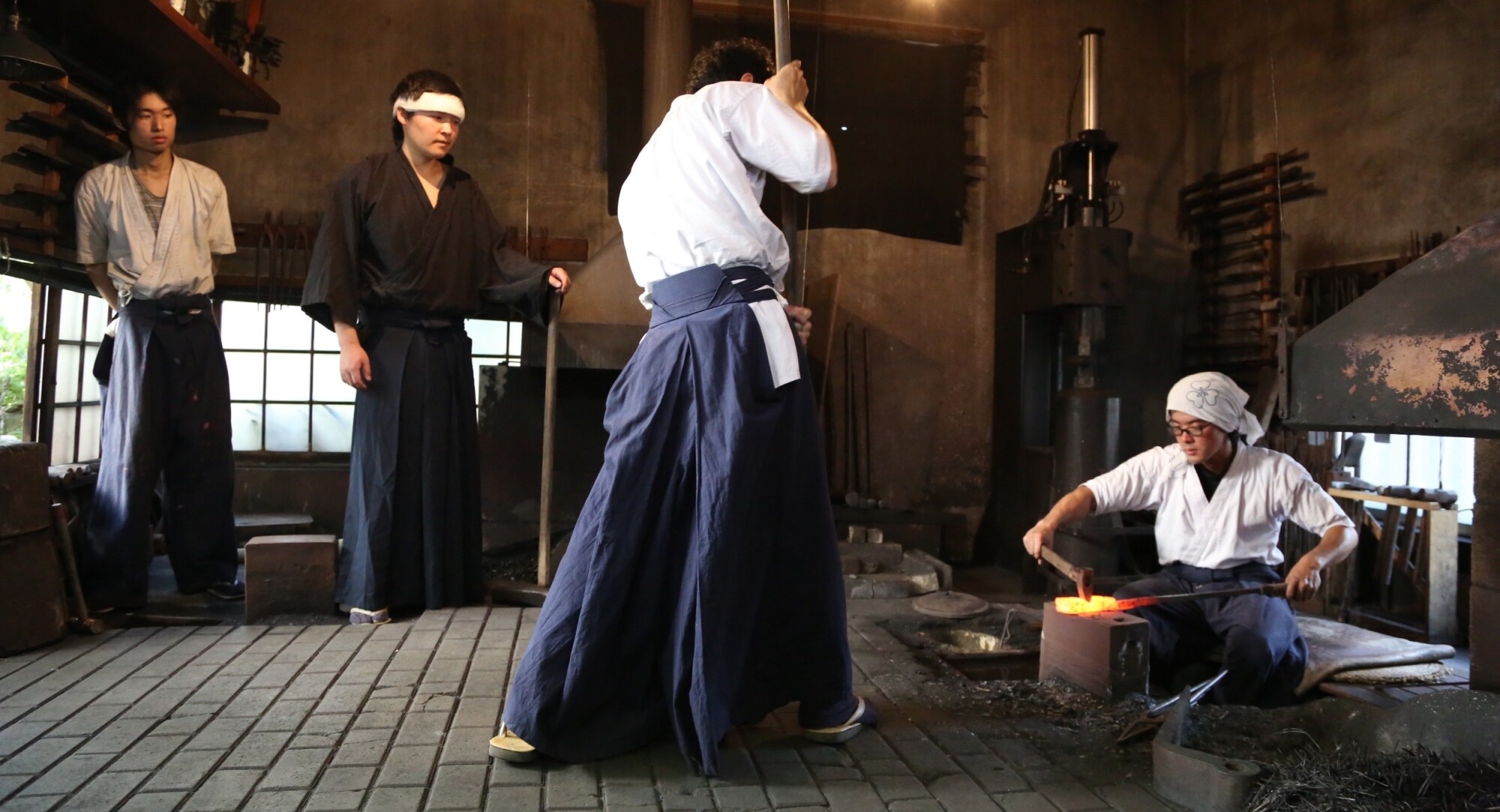
The Rhythm of the Hammer
As the rare, low-impurity steel glows with the intensity of the meticulously-tended forge, the swordsmith’s hammer falls in a mesmerising cadence, each calculated strike compressing the folded layers and shaping the blade’s distinct curvature. This rhythmic hammering, known as tsukibori, is a ritual as ancient as the art itself, a physical manifestation of the swordsmith’s mastery over forging prestigious steel alloys.
The tempo and precision of each hammer blow is crucial, as it determines the blade’s coveted distal taper, curvature and overall balance, ensuring it is not merely a formidable weapon but also an extension of the warrior’s arm and a work of art imbued with the swordsmith’s vision.
Once the blade has taken its distinct shape through hammering, it undergoes an intricate tempering process designed to impart a masterful balance of hardened and flexible regions by selectively introducing alloys like chromium. The sword is carefully cycled through precise heating and radically-cooled clay baths, creating the rippling hamon pattern unique to Nihonto blades.
This undulating hamon, revealing the interplay of hardened edge and flexible spine, is the defining hallmark of the swordsmith’s consummate skill and a testament to their mastery over strategic alloy introduction and tempering. It is this delicate balance of hardness and plasticity that gives Nihonto their legendary cutting ability, resilience and prized visual aesthetics.
The Finishing Touches
After the critical tempering phase is complete, the blade undergoes a series of meticulous finishing steps, each one a testament to the swordsmith’s dedication to perfection. Through expert polishing, engraving and delicate handling, the full visual splendor of the folded, tempered steel is revealed, replete with the distinctive hamon pattern and any chosen horimono etchings.
Then, the blade is deftly mated with a beautifully crafted tsuba (handguard) and meticulously wrapped with laborious the tsuka (hilt), ensuring superior grip, handling and aesthetic prestige befitting a Nihonto’s heritage. Every component, from the carefully-layered steel to the ornamental details, must be painstakingly treated to protect the blade’s legendary cutting edge and surface integrity.
The Soul of the Blade: Exploring the Spiritual Dimensions of Nihonto
Beyond the immense technical mastery involved in forging a Nihonto, there exists a profound spiritual dimension that is inextricably intertwined with the blade’s essence. Each Nihonto is believed to possess a transcendent soul, an amalgamation of the swordsmith’s spirit, the purified steel’s mystic essence, and the centuries of tradition that have shaped this revered craft.
This soul is reverently imbued into the Nihonto through a series of intricate rituals and consecration ceremonies steeped in the tapestries of Shintoism, Buddhism and Japan’s ancient smithing traditions. Swordsmiths invoke the blessings of deities, offer purification rites, and pour their most profound intentions into their work, ensuring these supreme blades are not mere instruments of violence but enlightened embodiments of the honourable budo philosophy.
Many Nihonto bear intricately-carved horimono etchings holding deep spiritual symbolism, often depicting auspicious imagery like dragons, sacred geometry and Buddhist calligraphy. These inscriptions, painstakingly carved into the folded steel’s hardened surface, are talismans imbuing the blade with a higher, transcendent essence.
The consecration rituals a newly-forged Nihonto must undergo are pivotal rites of passage. Under the guidance of revered priests and metal smiths, the blade is ceremonially blessed, its spiritual essence awakened through sacred smoke offerings, calligraphic inscriptions andancient ritualistic chants.
Through this solemn process, the Nihonto transcends its origin as a raw amalgam of purified metal alloys. It becomes a living embodiment of the samurai’s uncompromising honor, a talisman anchored in the ceremonial warrior traditions of millennia past, and an indivisible extension of the swordsmith’s spiritual force.
The Legacy of Nihonto: Preserving a Priceless Heritage
The true value of a Nihonto transcends its physical worth and origin as forged steel; it emanates from the blade’s hallowed legacy as a quintessential embodiment of Japanese artistry and the nation’s unbroken spiritual reverence for the sword over centuries.
These extraordinary swords, once reserved for samurai warriors of legendary status and peerless martial virtue, now reside as priceless centrepieces in collections worldwide. Their astronomical values, often reaching into the tens of millions of pounds, are a reflection of their paramount rarity and unmatched mastery of arcane forging techniques dedicated to removing all impurities.
Among the most coveted and invaluable Nihonto swords are those forged by the legendary smiths of the Kamakura and Muromachi periods, including transcendent masters like Masamune, Muramasa, and Yoshimitsu. These blades, crafted through obscure protocols for removing segregation impurities and infusing specialised alloys, while upholding the spiritual aspects of the craft, are considered the unsurpassed apex of Japanese swordsmithing. They are feverishly sought after by collectors and institutions for both their metallurgical marvels and embodiment of philosophies that defined the chivalric bushido code.
Preserving the Tradition
In an effort to preserve this priceless heritage and maintain provenance of techniques refined over millennia, the Japanese government has implemented comprehensive regulations and rigorous certification processes for authenticating true Nihonto swords. These measures, overseen by preeminent bodies like the Nihon Bijutsu Token Hozon Kyokai (Society for the Preservation of Japanese Art Swords), employ cutting-edge metallurgical analyses to scrutinise blades for the hallmarks of legendary forging schools and detect any modern mimicry attempts.
These initiatives help shield the legacy of Japanese swordsmithing by distinguishing genuine, spiritually-imbued Nihonto from the profusion of counterfeits lacking the intricate alloy formulations, layering and ceremonial consecration of the original art form. Only through these sanctioned authentications can the transcendent legacy of the Nihonto be stewarded for future generations.
The Kindred Spirit: Exploring the Connection Between Swords and Kitchen Knives
While the forging of legendary Nihonto swords and the creation of Japanese kitchen knives may initially appear worlds apart, the two disciplines share a profound, intrinsic connection rooted in the very essence of Japanese metallurgy and blade-making traditions.
Just as the samurai’s Nihonto was a sacred embodiment of their honor and battlefield prowess, the Japanese kitchen knife, whether a sublime santoku or versatile gyuto, reflects the chef’s mastery of their culinary craft. These knives, like their hallowed sword brethren, are rendered from the same rich tapestry of heritage and traditional techniques, meticulously forged by artisans who uphold the ancient wisdom passed down through generations.
While the forging process for kitchen knives need not be as protracted or reverently ceremonial as that of Nihonto, it nonetheless embodies the same principles of meticulous attention to detail and a profound respect for purifying steel and the ancestral traditions involved.
Akin to their sword-making counterparts, knife artisans carefully select and layer the finest Japanese steel varieties, rendering them free of impurities through masterful folding and heating protocols. This produces a blade that is exquisitely sharp yet remarkably durable and resistant to chipping or erosion from acidic foods.
The Spiritual Essence
Transcendent Nihonto swords are imbued with a spiritual essence; so too do Japanese kitchen knives carry within them the immaterial soul of their creators. These blades are no mere culinary tools, they are spiritually-resonant extensions of the artisan’s own force, rendered with reverence and meditative dedication akin to that which defined exalted swordsmithing for centuries.
Artisans pour their mastery, passion and utmost discipline into every kitchen knife they forge, imbuing each blade with a unique energy signature that harmonises with the chef destined to wield it. Like Nihonto of antiquity, these knives transcend their material composition, embodying the very essence of Japanese artistry, heritage and ceremonial zeal.
The Oishya Connection
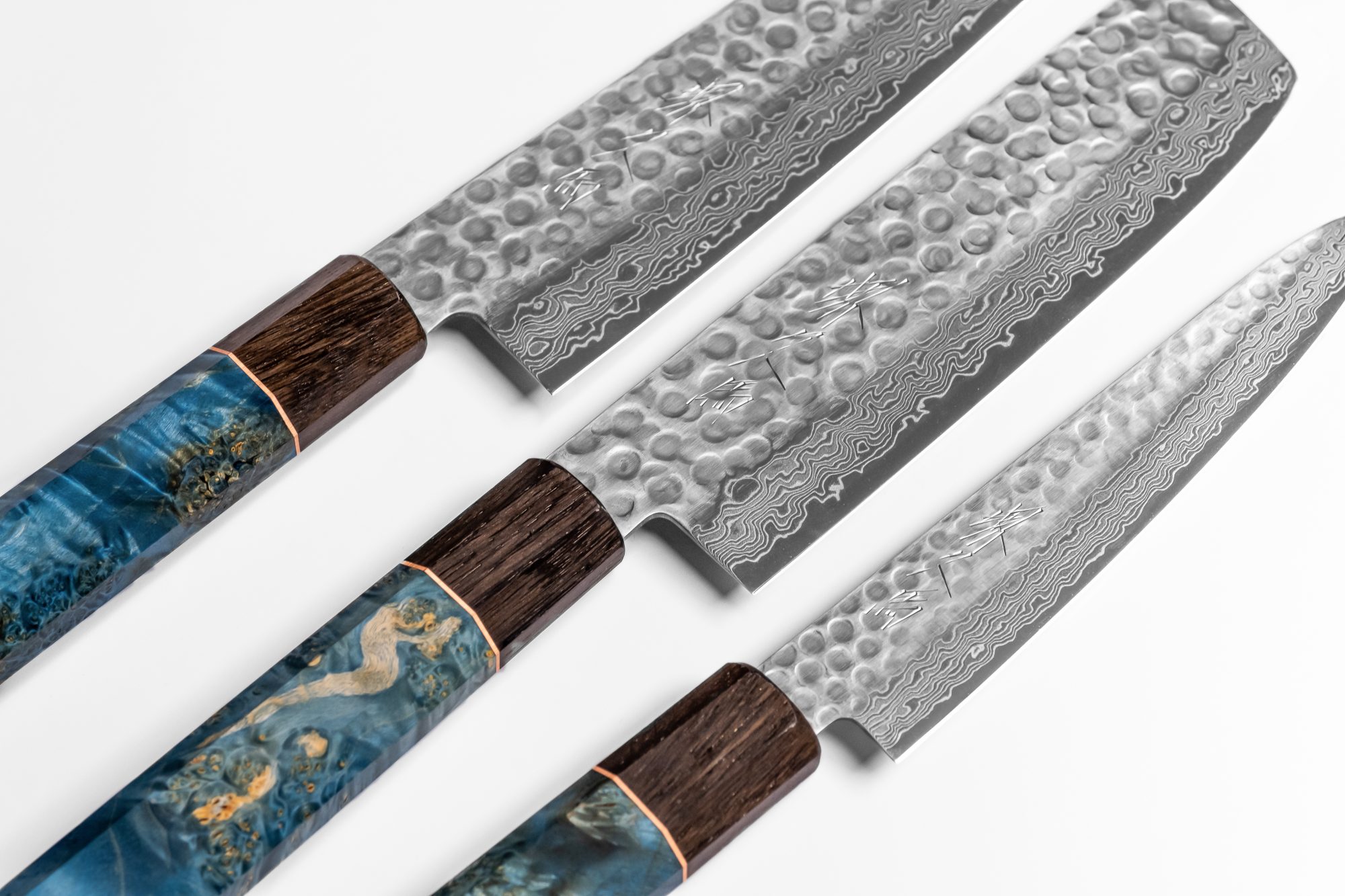
At Oishya, we understand the profound, transcendent connection between the exalted art of Japanese swordsmithing and the creation of our premium kitchen knives. Our artisans forge each blade while drawing upon the same hallowed well-spring of heritage and craftsmanship that birthed the most legendary Nihonto. With utmost care and ceremonial reverence, every Oishya knife is rendered as a true embodiment of Japan’s enduring blade-making legacy. Our knives are no mere culinary instruments; they are spiritual embodiments of the implacable samurai ethos, infused with honor, discipline and the same unwavering dedication that defined the legendary swordsmiths of antiquity. To wield an Oishya blade is to hold a piece of living history, a tangible connection to the centuries of mystically-imbued metallurgy and sword artistry that shaped Japan’s cultural identity.
Within the revered realm of Japanese metal smithing, the forging of Nihonto swords and the creation of premium kitchen knives are spiritually and technically intertwined – bound by a shared ancestral heritage, a ceremonial pursuit of perfected steel purification, and a profound reverence for imbuing blades with the essence of ancestral tradition.
Whether destined for the heat of ritual battlefield combat or culinary mastery, these blades transcend their role as tools, instead serving as enlightened embodiments of Japan’s rich cultural legacy. They are infused with the indomitable spirit of the artisans who forged them through mastery of ancient techniques and the most meticulous protocols for removing all impurities.
At Oishya, we are devoted to upholding this sacred, millennia-spanning tradition. Our knives are not merely exceptional in their technical metallurgy and cutting ability, but imbued with the spiritual grandeur of Japan’s ancient sword-making lineage. With each blade we reverently forge, we honor the esteemed legacy of those transcendent artisans whose arcane genius birthed the most priceless Nihonto the world has ever known.
We also highly recommend you to watch this fascinating video from Veritasium, that documents the whole process of katana making: